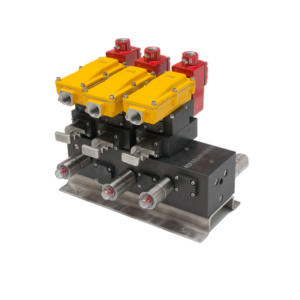
2oo3 with 3 SOV Solution
In industrial automation, the Safety and Availability of critical systems are of utmost importance. A key element in ensuring these systems operate smoothly and securely is the solenoid valve. Solenoid valves play a crucial role in controlling fluid flow in automated valve operations, directly impacting the overall efficiency and safety of industrial processes.
Redundancy is a well-known strategy for enhancing system Availability, but it often comes with its own set of challenges, such as increased complexity and the risk of spurious operations. This is where the 2oo3 (Two out of Three) redundant solenoid valve configuration shines. By employing a voting system where two out of three solenoid valves must agree to perform an action, this configuration strikes a delicate balance between Safety and Availability.
The 2oo3 configuration significantly reduces the Impact created due to one error in any of the electrical loops., ensuring that the system only shuts down or initiates an action when absolutely necessary. This not only enhances operational safety but also minimizes unplanned downtime, which can be costly for Process industries.
Rotex engineers have taken this concept a step further with the development of the 5th generation 2oo3 configuration. By leveraging advanced diagnostics and online maintenance capabilities, We created a solution that not only improves Safety and Availability but also simplifies maintenance and reduces operational costs. This innovative approach ensures that industrial systems can achieve unparalleled performance, Availability, and Safety, making it an essential component for modern Critical Automated Processes.
1st Generation of safety with redundancy
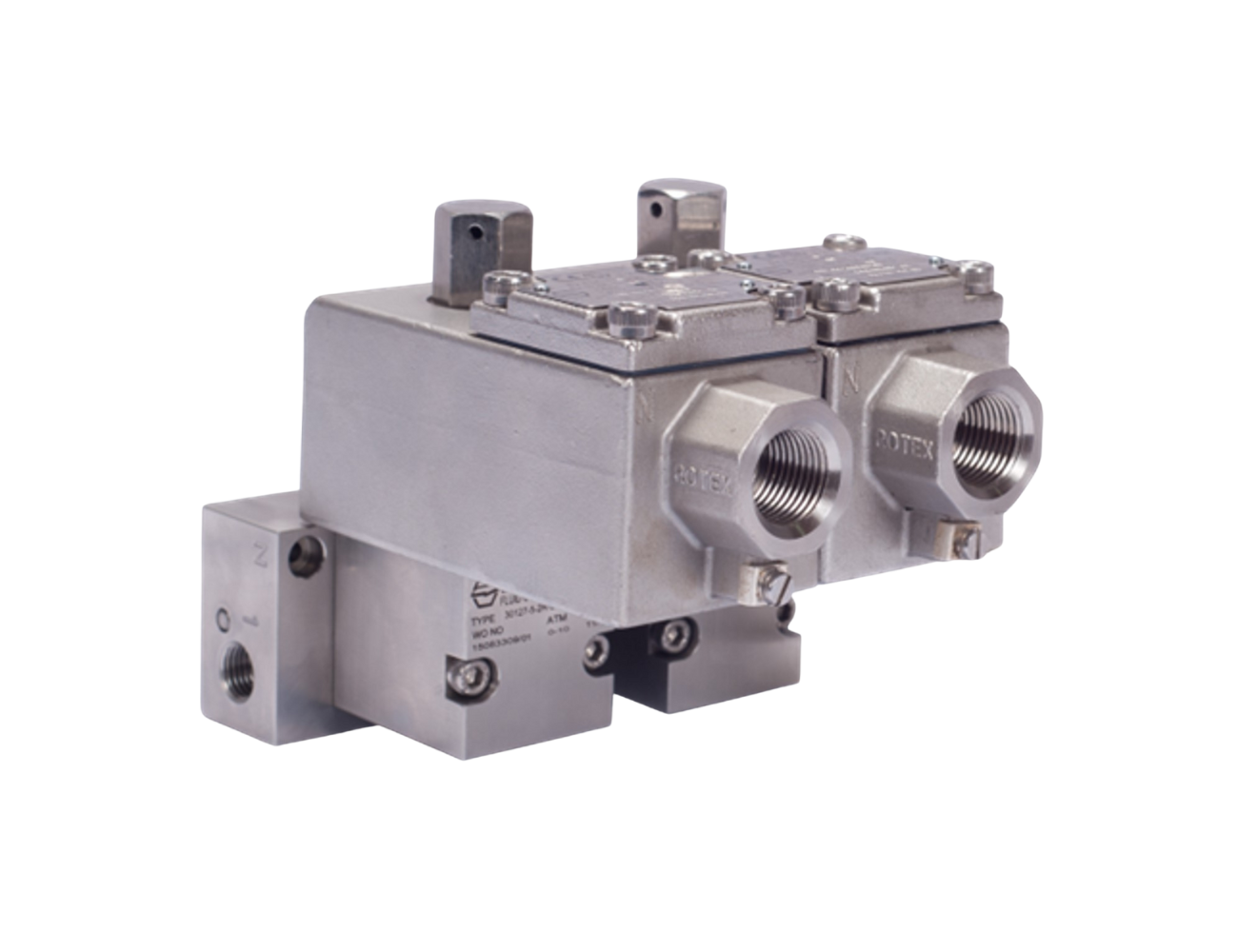
The first generation of safety systems relied heavily on redundancy to improve operational safety. While redundancy mitigated the risk of system failures, it inadvertently doubled the chances of spurious operations. Solenoid valves, essential for critical automated valve operations, were often configured redundantly. However, the reliability of other components, such as cables, relay junctions, and power sources, also played a crucial role. Failures in any of these components in the loop could lead to system failures, necessitating their redundant configuration as well.
Despite the redundancy, frequent verification was required to ensure it was intact. Any failure in one element could render the system unreliable due to loss of redundancy, necessitating regular checks during plant shutdowns as a part of preventive maintenance. This posed a risk of spurious shutdowns or safety risks during operations.
2nd Generation of safety with redundancy and detection (predictive maintenance)

As there was a need for frequent checks to maintain redundancy at the same time, online redundancy checks were risky thus there was a need for predictive maintenance and online maintenance of both elements. Thus 2nd Generation solution came into the picture with a 2oo2 configuration which now detects any loop element failures through predictive maintenance
Although 2nd Generation Redundant solutions provided the most safety but at the cost of frequent spurious failures. As any valve still failing causes a safe but spurious failure.
Such incidents cost the industry huge downtime which amounted to Over 100K USD loss per incidence. Although safe operation reliability increased to 100X but spurious shutdowns just doubled.
3rd Generation of safety with 2oo3 configuration
Safety with reliability
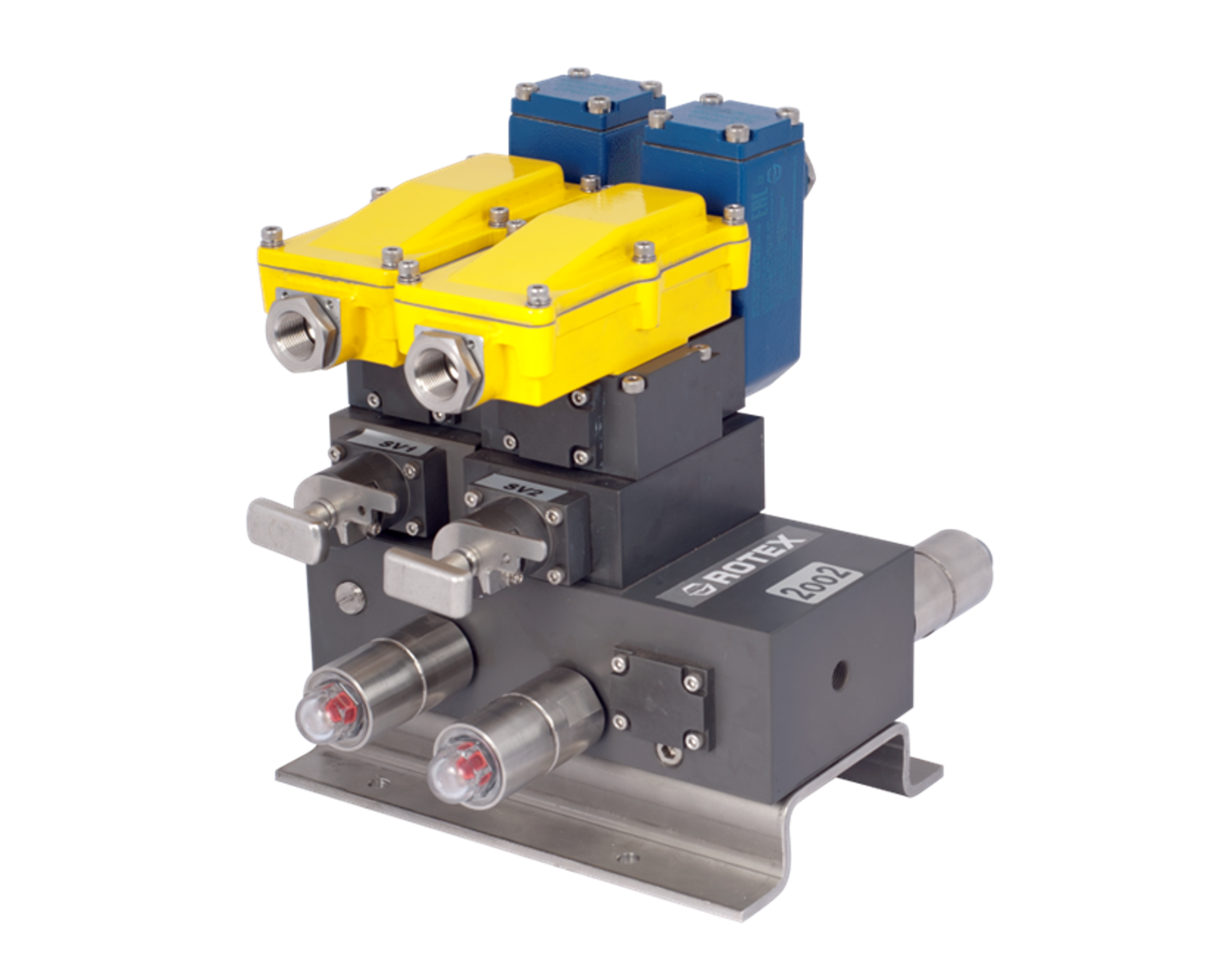
The third generation introduced the 2oo3 configuration, also known as the Two Out of Three voting system. This configuration offered a balanced solution, improving safety (though not as much as the 2oo1 configurations) and Availability by approximately 32.9X.
This configuration provides higher safety (but around 1/3 that of 2oo1 configuration of 2 element system but still considerably higher compared to a single solenoid system) but also provides considerably higher Availability (around 32.9 times better as per the design you choose) and thus preventing any spurious/ unplanned trips.
There are quite a few solution available in the market which achieve 2oo3 configuration with the use of 4 solenoid valves. The basic version is without diagnostics or online maintenance feature and thus it suffer similar issues like 1st Generation solutions. Also compromises are quite higher on safety
4th Generation of Safety with 2oo3 Configuration
Diagnostics & Online Maintenance with 4 Solenoid Valves
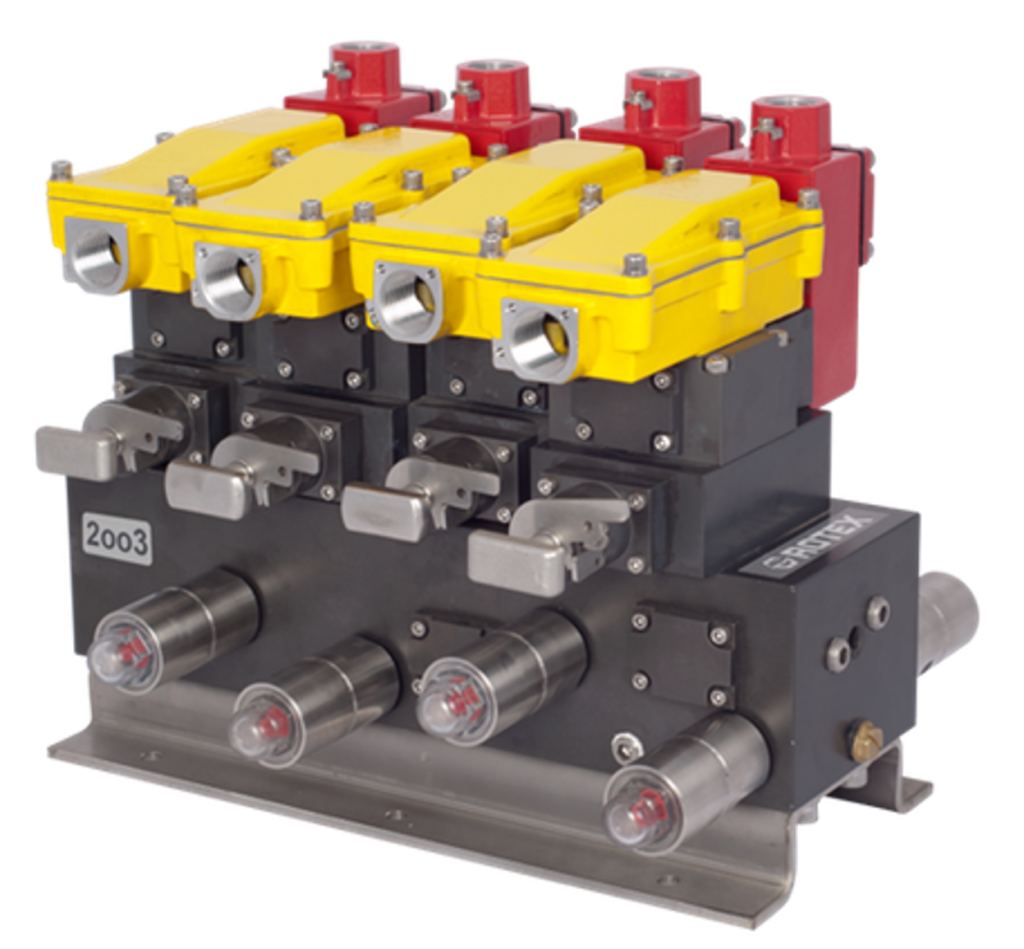
To address diagnostic and online maintenance challenges, the fourth generation introduced designs with self-diagnostics using pressure or position sensors. In this setup, each solenoid valve is individually monitored, allowing them to be put into Isolation mode and serviced without bypassing the entire system. This capability facilitates online maintenance.
This configuration requires two of the four solenoid valves to be connected to a single channel, specifically solenoid valves 1 and 4. Any other combination would compromise the 2oo3 output. This requirement complicates installation and maintenance, as there is no way to detect and correct possible failure configurations easily.
Using four solenoid valves increases the probability of two valve failures compared to a three-valve system. Additional diagnostics, inputs to the Distributed Control System (DCS), and cabling further elevate the potential for device failures. The presence of more components in the pneumatic circuit loop slightly compromises product safety.
Moreover, the situation becomes problematic when operating through intrinsically safe barriers, as a single barrier may not provide sufficient current for all solenoid valves, leading to a compromised 3oo4 configuration. Increased components result in higher maintenance demands, causing the system to spend more time in a bypass mode. In this compromised state, the system's safety and reliability can decrease by 50% to 66% compared to normal operation.
To Achieve Safety & Reliability with Diagnostics & Online Maintenance, Rotex Engineers Developed 5th Generation 2oo3 Configuration Through 3 Solenoid Valves
5thGeneration: Advanced 2oo3 Configuration with 3 Solenoid Valves
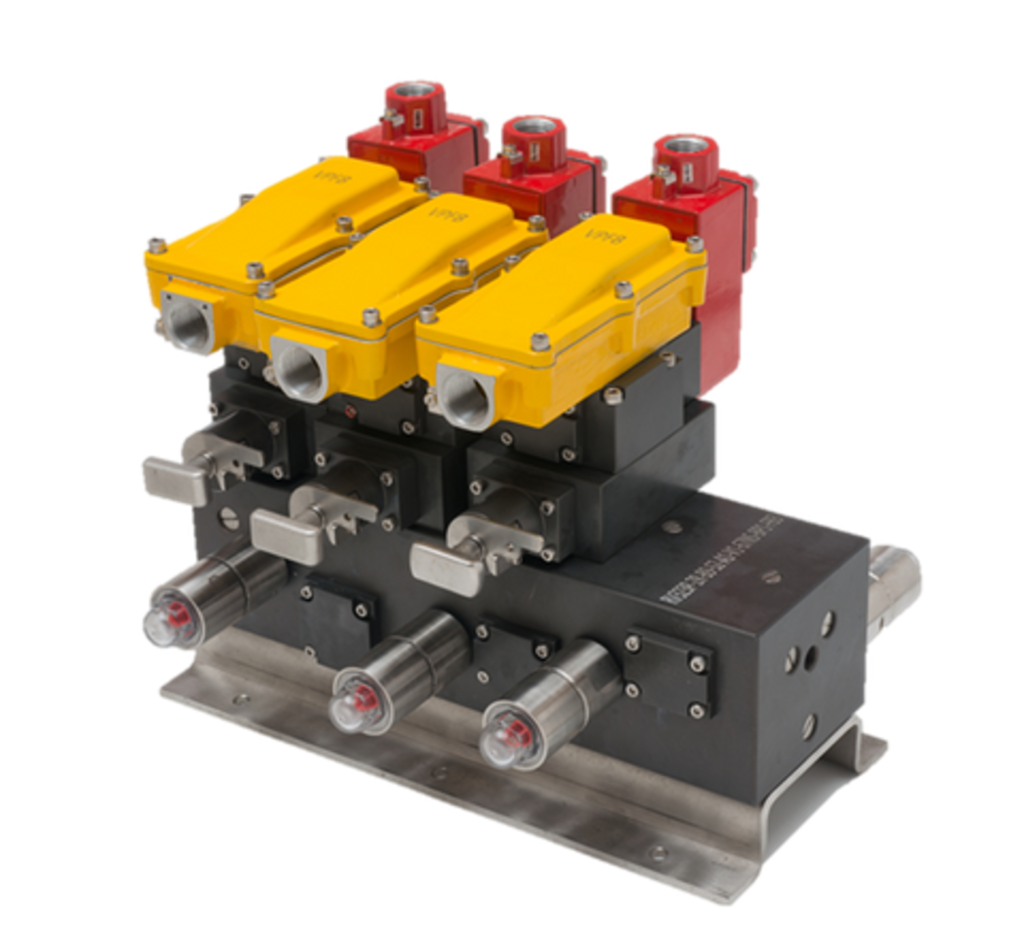
The fifth generation of safety solutions revolutionized the 2oo3 configuration by utilizing only three solenoid valves. This innovation, patented by Rotex, improves reliability by over 33.1% and safety by 0.7% compared to four-valve systems. It simplifies diagnostics, reduces cabling and maintenance complexity, and is ideal for intrinsically safe applications.
Benefits Of Rotex 5th Generation 2oo3 Configuration
More reliability as compared
to 4 SOV system.
lesser Maintenance
Save 3-5 Lakh
INR 3-5 lakh savings per system with streamlined efficiency: fewer cables, optimized communication, minimal maintenance, and increased uptime.
Error Proof
Unlike 4 Sov system where 2 Sov to needs to be connected on single channel which invariably creates confusion and chances of error. 3 Sov 2oo3 configuration is error proof
No wiring error
0.7% more safer
True 2oo3 with
Exia Sov
Lesser Capital cost
100% higher safety & reliability with intrinsically safe solenoids
Lower false alarms lead to lower risks
Take Action: Enhance Your System's Safety and Reliability Today!
Don’t let outdated safety configurations put your critical systems at risk. Upgrade to Rotex’s 5th Generation 2oo3 Solenoid Valve Configuration and experience the next level of safety, reliability, and efficiency.
Schedule a consultation with our experts.
Contact Us Today!
Discover customized solutions tailored to your specific needs